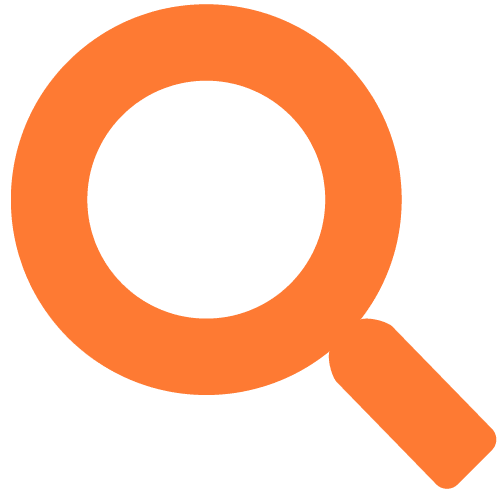
NDT Services
We make use of a wide range of NDT inspection methods, including Radiographic Testing, Ultrasonic Testing, Magnetic Particle Testing, Eddy Current Testing, Phased Array Ultrasonic Testing, Visual Testing and Dye Penetrant Inspection.

Accreditations
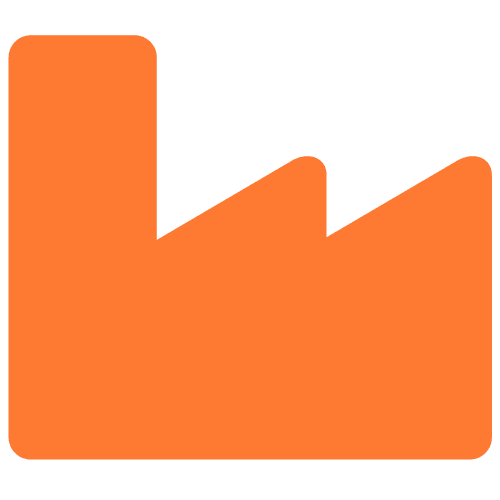
Industries Served
We provide a range of non-destructive testing services for a variety of industries including Aerospace, Automotive, Construction, Energy & Power Generation, Engineering, Petrochemical, Civil Engineering, Foundries & Forging and Motorsport.
Capital NDT has over 35 years of experience
OUR ACCREDITATIONS

Welcome To Capital NDT
Capital NDT is a UK based, independently owned organisation that specialises in non-destructive testing. We provide non-destructive examinations at both our laboratory & testing facility and on-site across the UK.
Our state of the art testing facility is located in Colnbrook, which is conveniently located within minutes of the M25, M4 and M3 motorways. Our UKAS accredited laboratory for radiography is equipped and prepared to meet the requirements of our customers from a wide range of industries.
Our on-site NDT services division is fully equipped to carry out all non-destructive testing methods anywhere in the UK. Staffed by experienced and trained personnel who all hold PCN’s, the division provides NDT services on a contract or day to day basis and has the backing of our laboratory quality control systems and procedures.
How can we help you?
Contact us today to find out how Capital NDT can help you with our wide range of non-destructive testing services.
What Is Non Destructive Testing Used For?
NDT is a non-destructive evaluation and analysis technique that is used in a number of industries to detect and evaluate the properties of a material or component and detect any flaws or defects without damaging the parts.
NDT makes use of a wide range of testing methods combined with visual examination to provide condition monitoring and materials testing services. Each NDT technique is used to achieve different goals such as weld testing or to measure material thickness.
Non-Destructive Testing Methods
We make use of a range of NDT methods and testing techniques to provide quality control and non-destructive examination services to our clients. Including:
Dye Penetrant Testing:
Eddy Current Testing:
Eddy Current Testing is an NDT method that is commonly used to detect surface and near-surface flaws in conductive materials. This testing method is used in a range of industries, including aerospace, rail, manufacturing and automotive. The testing equipment used for Eddy Current Testing is light and compact, allowing for on-site testing across the UK.
Magnetic Particle Inspection:
This method of NDT is used to find surface and near-surface flaws in ferromagnetic materials by using a powerful magnet to create a magnetic field around the specimen. A sensor is then used to detect the magnetic flux leakage that is generated around flaws such as cracks.
Phased Array Ultrasonic Testing:
Phased Array Inspection is an advanced testing method that is used to detect flaws that cannot be found with conventional NDT methods such as Radiographic Testing or manual Ultrasonic Testing. Phased Array testing is capable of meeting the higher demands of advanced industries and services that we work with.
Radiographic Testing:
Radiographic Testing is commonly used to detect internal and sub-surface irregularities in a range of components. Radiographic Inspection makes use of X-rays to inspect for flaws and discontinuities. The results are then processed on to a physical film for visual inspection by a trained radiographic interpreter. We can also digitise the image with our top of the range radiographic film digitiser which creates a digital radiography image that can be viewed on your own computer. This testing method provides a permanent photographic record of testing.
Testing Metal Bar Stock
Bar stock must be produced in accordance with AMS-STD 2154 or ASTM E2375 and it is a requirement that ASTM E127 standard calibration blocks are used. The bar stock will eventually be made into a component, the structural integrity of which cannot be confirmed unless it has been tested prior. Any and all engineering calculations can be invalidated by a fault in the bar stock used.
Ultrasonic Inspection:
This NDT method is used to test for any internal defects and flaws in castings, forgings and welds. It can also be used for material thickness measurement. It works by sending sound waves into a material and watching how the guided waves interact with the material. Ultrasonic Testing is particularly useful in examining pressure vessels in service for power generation.
X Ray Film Digitisation and Duplication
Using our Radiograph Digitisation System and a computer we are able to create a copy of your X-Ray that can be uploaded to your computer system for storage or transfer. We are also able to duplicate and print X-Ray films, providing you with an exact reproduction that can be viewed with a traditional lightbox.
For More Information On Our NDT Inspection Services
For more information on any of our non-destructive testing services contact our team by calling us on 01753 684 896
or by filling out our contact form: